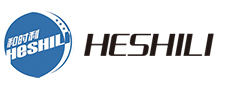
PBT can be used to spin civilian or industrial filaments by the traditional melt method. It is not only suitable for conventional spinning, but also suitable for high-speed spinning to produce fine special filaments. It can also be combined with PET or polypropylene for composite spinning or polypropylene , Polyamide and PET are blended and spun to improve the elasticity and dyeability of polyester, polypropylene or nylon. The intrinsic viscosity [η] of PBT suitable for spinning is 0.6 to 1.6. When [η] is less than 0.6, filament breakage is likely to occur during spinning; when [η] is greater than 1.6, the melt viscosity is too high and spinning is unstable. If the melting point of PBT is around 223°C, the spinning temperature should be 30-65°C higher than the melting point, that is, 260-290°C. If the spinning temperature is higher than this temperature, PBT will easily be thermally decomposed.
The spinning speed is usually higher than 1100m/min, so that the nascent silk has a relatively complete fiber structure, and the structure is strengthened in the post-drawing process, so that the final fiber has better properties. If the spinning speed is lower than 1100m/min, the shrinkage rate between the godet rollers is negative, that is, automatic elongation, and because the crystallization speed of PBT fiber is 10 times faster than that of PET, the fiber starts to crystallize, forming incomplete crystals. The fiber structure is quite unfavorable for post-stretching. In addition, due to the high-speed crystallization of PBT fiber, it is not suitable for thermal drawing. Otherwise, the initial modulus of the fiber will decrease.
If the spinning speed is above 1500m/min, the fiber will have a shrinking force of crystal change (β-type→α-type), which will significantly deteriorate the winding form. Due to this shrinking force, the shrinkage states of the inner, middle and outer layers of the bobbin are different. That is, the middle layer of yarn can shrink by itself, while the inner layer of yarn and the outer layer of yarn, because their winding is restricted by the bobbin and the yarn pressure is small, it is difficult to wind tightly. Therefore, the silk has a certain property difference between the layers, and the dyeing of the finished silk is likely to be uneven in the subsequent stretching or stretch deformation processing.
In order to reduce this difference in shrinkage, it can be eliminated by adjusting the winding tension. The shrinkage is given between the godet rollers or between the godet roller and the winding roller. That is, on the same spinning machine, spinning at a spinning speed higher than 1500m/min, followed by 1.1-1.9 times cold drawing, and then performing tension heat setting or relaxation heat setting to achieve the purpose of controlling the self-shrinking of the fiber , And then wind up. At the same time, since the reason for the fiber shrinkage is that PBT has a special crystal structure (α, β-type crystal modification), it is also important to control the ratio of its α-type crystal modification structure to the β-type crystal modification structure.
Official account